Chemical specialist SABIC has presented test results that demonstrate the potential of thermoplastic-based thermal runaway barrier solutions to help prevent fire spread within electric vehicle (EV) batteries.
Visitors to SABIC’s booth at the NPE2024: The Plastics Show in Orlando, Florida, this week are able to see the tested thermoplastic battery module box, which is on display in an area of the show dedicated to the BlueHero initiative supporting the automotive industry’s transition to electric power and a low-carbon future. Various EV battery components made with SABIC’s materials, including module enclosures, busbars and end plates, are also on display at the booth.
The test series conducted by SABIC at the sub-system level revealed that using a battery module box made from Stamax 30YH570 long glass fiber polypropylene (PP) resin, with an intercellular thickness as low as 1mm, could serve as an effective thermal barrier. This material, according to SABIC, demonstrates the ability to provide necessary thermal insulation and flame resistance, reducing the likelihood of cell-to-cell propagation during a thermal runaway scenario, thus helping to mitigate safety risks.
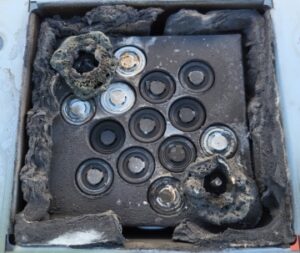
These recent findings build upon previous independent evaluations of SABIC’s Stamax 30YH570 resin, which in 2023 received the UL Verified Mark from Underwriters Laboratories for effective flame delay performance. The assessment, based on UL 2596, highlighted the material’s ability to delay flames effectively, particularly in battery enclosure applications.
The thermal runaway propagation tests conducted at NPE involved a cluster of lithium-ion battery cells enclosed in a steel chamber, with and without injection-molded Stamax 30YH570 resin blocks serving as a thermal barrier. In tests without the thermal barrier, thermal runaway led to hazards such as high-temperature gas, open flames, and pressure increases, propagating to neighboring cells. However, the presence of the thermal barrier effectively suppressed heat transfer and thermal propagation, ensuring the safety of the remaining cells.
Furthermore, SABIC is also presenting various EV battery applications at NPE that successfully use its thermoplastics. For instance, the battery module from the 2023 Hyundai Ioniq 6 incorporates SABIC polypropylene compound H1030 for module enclosures, designed to meet stringent fire safety regulations for EVs.
“We are pleased to share this additional validation of our thermoplastic solutions’ strong potential for use in EV battery components and systems,” said Fahad Al-Harthi, global director of automotive at SABIC Polymers.
“Our portfolio of flame-retardant materials, combined with our expertise in application design and fire-polymer interaction, can help enable new thermal runaway barrier approaches. We look forward to continued collaboration across the automotive value chain to help improve the safety, efficiency and performance of EV battery systems.”